Thermal management is an integral part of system design and requires different engineering disciplines in the overall design process. One of the most important reasons to use thermal data for LED-based product is to design in the reliability of the final product. Apart from adhering to certifications from Nationally Recognized Testing Laboratories like UL, CSA, & ETL, there are two factors of reliability that are considered when testing LED luminaires. The L70 lifetime of the luminaire projects when light output will have decreased 30%. This was devised because LED emitters are less likely to fail catastrophically than to simply dim. The second is the probable lifetime of the driver, which fails in the more normal catastrophic fashion. How do engineers conclude that LED lighting products perform to the standards at which they are marketed? They use a combination of internal and third-party testing to ensure the reliability every step of the way. Let’s dive deeper into the process of evaluating LED thermal management.
Thermal Testing of LEDs
National and international industry standards identify recommended testing methods for lighting products, many of which are conducted by third party testing laboratories. Some of the most critical lighting performance standards for North America are:
-
IESNA LM-79 – Optical and Electrical Measurements of Solid-State Lighting Products
-
IESNA LM-80 – Measuring Luminous Flux and Color Maintenance of LED Packages, Arrays, and Modules
-
IESNA LM-82 – Characterization of LED Light Engines and LED Lamps for Electrical and Photometric Properties As A Function of Temperature
-
IESNA TM-21 – Projecting Long Term Lumen Maintenance of LED Light Sources
In turn, there are several North American and international energy efficiency programs that have their own specifications. The more prevalent programs are Energy Star®, Natural Resources Canada (NRCan), California Energy Commission (CEC), U.S. Department of Energy (DOE), and DesignLights™ Consortium (DLC). Since specifications are different than defined standards, the criteria can vary depending on the individual program changes.
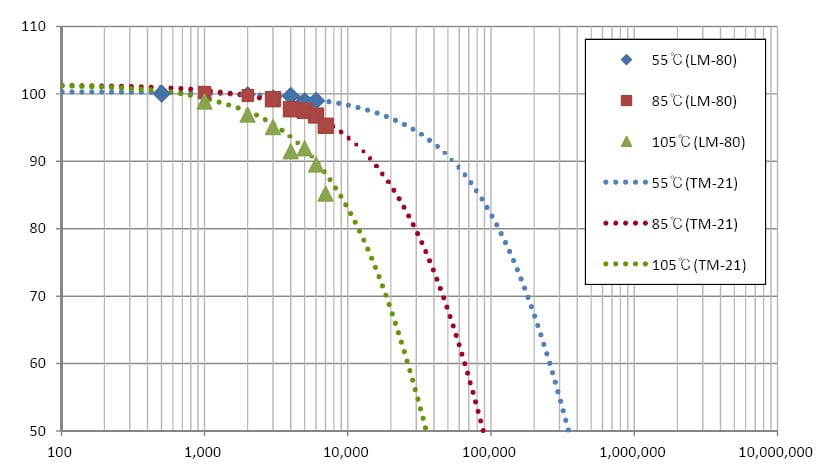
An example of a chart representing LM-80 and TM-21 data from LED module manufacturers.
LED manufacturers publish LM-80 data that estimates the lifetime of the LEDs at certain temperatures and currents. LED product engineers use the TM-21 method to extrapolate the L70 lifetime of the light engine. Throughout the development process, LED product engineers thermocouple LEDs to ensure that temperatures are reduced as much as practical to maximize their lifetime. Lifetime of the LED modules themselves are typically defined by two factors: drive current and junction temperature. A higher drive current means higher lumen levels but lower LED module lifetime. Once the drive current has been determined, the junction temperature can only be reduced by external factors like heat sinks, module-heat sink interface and ambient temperature surrounding the LED module. The higher the temperature, the lower the lifetime of the LED module. Because it cannot be directly measured, most manufacturers will specify a maximum case temperature (Tc) and maximum thermal resistance between junction to case by describing the manufacturing process. Taking all of this into account before actual production begins, all internal testing is validated by sending individual units to a third-party testing laboratory.
Thermal Testing of Power Supplies
Like LED manufacturers, power supply manufacturers publish their own lifetime curves based on the operating temperature of the device. The efficiency of the LED driver plays a key role in determining the thermal stresses inherent to the product design, which is a determinant in its lifetime and reliability. LED driver efficiency defines how much of the power drawn by the power supply is lost in heat. The more efficient the driver, the less heat is dissipated into the surrounding area which improves thermal management. Like the LEDs that are tested during development, power supplies are internally tested, validated, and then the complete fixture is sent to a third-party laboratory.
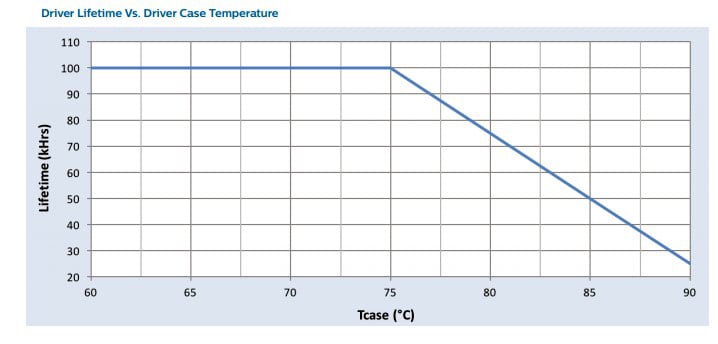
An example of a chart representing driver lifetime vs. external case temperature.
Additional Product Testing
Trustworthy LED product manufacturers employ the highest levels of quality, integrity, and conformance to regulatory requirements defined by North American and international standards. Evaluating lighting systems for safety, as well as performance, is critical. Product testing allows manufacturers the assurance what they have designed is indeed what their fixtures deliver. Below are some examples of testing capabilities that help provide reliable and accurate information to engineers for product development:
-
Goniophotometer – Typically the highest precision assessment and verification instrument for determining light intensity and distribution. This creates IES files that are standard for the lighting industry and allows architects and engineers to project light paths and determine layouts.
-
Integrating Sphere – Creates robust reporting of optical measurements such as CRI, CCT, and total luminous flux.
-
Rain Testing Chamber – Tests for IPX5, IPX6, and IPX9 ratings. It also performs UL 1598 rain tests to determine if certain LED luminaires are suitable for wet locations.
-
Settling Dust Chamber – Tests for Ingress Protection (IP) Ratings for IP6X.
For testing that isn’t done internally by the manufacturer, third-party testing plays a key role in product certification. Nationally Recognized Testing Laboratories (NRTL) are recognized by the Occupational Safety and Health Administration (OSHA) to test products to the specifications of applicable product safety standards. Their function is to provide independent evaluation, testing, and certification of any electronically operated product. NRTLs or other NVLAP® accredited facilities have equipment calibrated to ISO 1705 and can perform all the above testing to meet lighting industry standards and individual energy program specifications.
Want To Learn More?
US LED products are built to validated designs and engineered for ultra-long-life reliability. Aside from the rigorous testing done internally, our LED luminaires are independently tested and certified by NRTLs in North America for the quality assurance you’re looking for. This allows us to back our products by an industry leading 10-year warranty. Click below to get pricing for your next project and find out why US LED does the Right Things, the Right Way, and On Time! Click here to get your pricing.